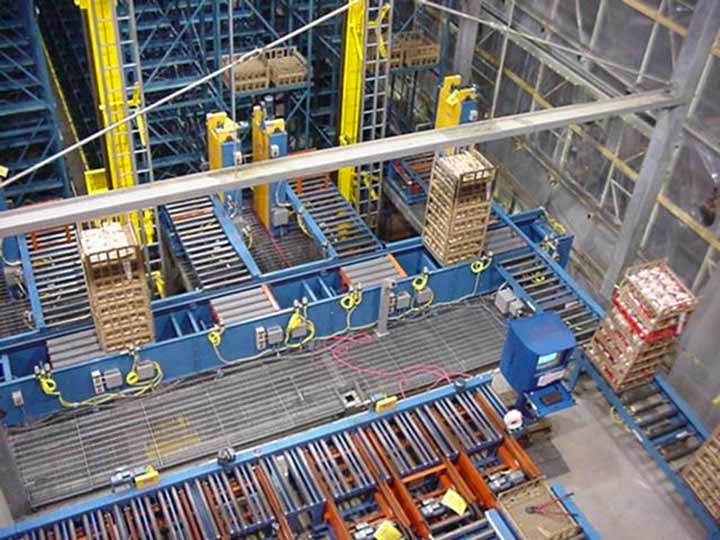
Whether your process requires transporting or accumulating empty pallets, or pallet loads up to 20,000 pounds, Lauyans EPS is equipped to meet your pallet handling needs.
Our pallet conveyors are used in transportation and accumulation operations in manufacturing, warehousing, and distribution.
- Increased productivity
- Flexibility of equipment layouts
- Safe handling of products
- Heavy duty capability
- Lower total cost of ownership
We have developed a multitude of pallet handling conveyors and related equipment for use in a wide variety of industries. From individual pieces of equipment to turnkey systems, including controls and installation, we can provide what you need.
Freezer Pallet Handling System
Lauyans EPS was contracted to supply and install a complete 2-level conveyor system designed to operate in a -20°F environment. Total system length is approximately 700 feet; and consists of CDLR Conveyors, Chain Conveyors, Vertical Reciprocating Conveyors, and custom designed pallet check stations.
The system input on the lower level includes custom designed pallet jack interface stations. Ten Storage / Retrieval Machine (SRM) interface spurs are provided on the second level.
Conveying System for Radioactive Waste
The scope of work for this project involved the design and fabrication of a conveyor system which is used to handle 1,200 pound drums (in several areas) and 10,000 pound boxes in another system.
The drums handled are re-classified containers of irradiated waste product that have been excavated, x-rayed and compacted before placing inside new containers for permanent disposal.
The boxes to be handled were an even greater challenge. Containers that are being excavated for processing on the box line are of undetermined design and footprint. This means the conveyor design must accommodate and convey boxes that are unknown as far as their quality and ability to be conveyed. Boxes are eventually raised to a second level where they are cut open, emptied and shredded/compacted.
Many of the rooms in this system are limited access; and can only be entered in sealed full body protective suits. Some rooms are Class & Division rated (explosion proof). Because of these extreme limitations, the customer required that this conveyor be extra-heavy duty design with ultra-low maintenance requirements.
Poultry Processing
A partial view of a large material handling system that the Lauyans EPS team designed and installed in a poultry processing facility.
This conveyor receives stacked baskets of product from the processing plant (inside a cold room environment) and conveys them through a blast-freezing operation. After the blast-freezer, the containers are routed to a four-aisle Automated Storage / Retrieval (AS/R) system.
Upon call from the host computer, loads can be automatically routed from the output spurs of the AS/RS to the order picking and processing area. Lauyans EPS designed multiple ergonomic packing stations to aid the system operators in this area.
Forklift Mast Production with Custom-Designed Pallets
The Lauyans EPS team was presented with a challenge from a major forklift manufacturer. The challenge involved receiving long, heavy beams (used for truck masts) and delivering these beams to various machining centers for fabrication (notching, machining, welding, etc.)
The customer came to us with a basic flow-path diagram, and requested that we assist them in the development of a processing system.
Lauyans EPS developed a synchronous conveyor system that uses a special pallet for transferring the loads between work cells. The custom pallet makes repositioning and turning of the beam a lot safer and easier for the operator than any previous methods used.
Side-By-Side Container System
An automotive manufacturer required a system to queue empty steel containers used in processing chassis components.
The lane on the far right is the empty container input conveyor. Loads deposited by a forklift operator will automatically feed a filling position (in the background). As a filled container exits the filling position, any queued containers will automatically advance to keep this station supplied with containers.
The PLC system automatically routes the filled container to the correct lane (one lane for LEFT side components, the other for RIGHT side). Again, these containers are automatically queued to the forklift pick-up position with zero-pressure accumulation logic.
Dry-Goods Distribution Center
A major dry-goods distribution center uses Lauyans EPS technology to automatically classify, square and weigh loads which are inbound to an AS/RS. Loads that are deemed as “rejects” are automatically routed to an appropriate area for repair. We have provided a total of ten Receiving Cells for this customer over an eight-year period.
In the latest system design, multiple receiving cells were equipped with an “automated repair” function. If a pallet is rejected due to bad bottom boards or excessive deflection, it is routed to a repair zone. In the repair zone, a slave board is automatically dispatched to the repair position where the load is automatically lifted momentarily so that this repair board can be positioned under it. The load may now proceed to the SRM input level for induction.
Tell us about your project.
Our goal is to not only provide the equipment you need, but to help you develop a comprehensive solution.
In designing your custom conveyor system solution, we focus on your needs, your business, and your budget.